Revealed: The Secret Science Behind Your Favorite Sheet Masks (From Lab Bench to Luxury)
Ever wonder how that drenched, silky mask transforms dull skin into dewy radiance overnight? Spoiler: It’s not magic – it’s micro-engineering. As pioneers in clean-beauty manufacturing, we’re pulling back the curtain on how lab-crafted, skin-optimizing masks go from raw ingredients to your selfie-ready glow. No hype, just hydrogels.
Why Mask-Making Is Skincare Alchemy
Unlike creams, masks demand triple-phase synergy:
- Bio-compatible fabrics that grip 30x their weight in serum
- Stable actives that penetrate without preservatives
- Eco-smart packaging that locks freshness guilt-free
Step 1: The "Eureka!" Formula Lab
Our chemists blend skin-identical actives using:
- Cold-Process Emulsification: Mixing oils/waters at 5°C prevents nutrient degradation
- Nanofiltration: Removing particles >0.22 microns for crystal-clear serums
- Phyto-Retinols: Plant-derived collagen boosters (bakuchiol/ rambutan extract)
"Like crafting liquid silk – every batch pH-tested 12x."
Step 2: Biodegradable Sheet Engineering
Not all mask fabrics are created equal. We use:
Material | Source | Skin Benefit |
---|---|---|
Tencel™ | Eucalyptus pulp | Hypoallergenic, 50% more breathable |
Bio-cellulose | Coconut water | Nano-fibers hold serum 300% tighter |
Seaweed Fiber | Kelp extract | Dissolves in compost releasing minerals |
(Microscopic view: Seaweed fibers creating "serum reservoirs")
Step 3: Sterile Serum Fusion
The critical moment – infusing sheets with active serum:
- Vacuum Impregnation: Sheets sealed in chambers suck serum deep into fibers (-0.8 ATM pressure)
- Ultrasonic Bonding: Sound waves bind actives to cellulose at molecular level
- Flash-Freezing: -30°C blast sets serum structure in 8 seconds
Result: 0.3ml precision serum loading per sheet (±0.01ml variance)
Step 4: Zero-Waste Packaging
Masks stay potent because we:
- Flush with Nitrogen: Removes oxygen to prevent oxidation pre-seal
- Plant-Based Films: Sugarcane-derived pouches (decompose in 180 days)
- Soy Ink Printing: Non-toxic, water-soluble pigments
Step 5: Robo-Precision Assembly
Watch ABB Robotics arms:
- Unfold sheets at 400 masks/minute
- Laser-cut eye/nose openings within 0.1mm accuracy
- Seal pouches with ultrasonic welding (no glue needed)
Step 6: Rigor & Responsibility Checks
Every batch passes:
- Stability Chambers: 60-day cycle testing (from -5°C to 50°C)
- TEWL Scans: Measures if barrier repair claims hold (avg. -32% water loss)
- Eco-Audits: Carbon footprint <0.8kg CO² per 100 masks
Why This Matters for Your Skin
Precision manufacturing equals visible results:
- 72-hour hydration from multi-weight hyaluronic acid chains
- No “mask burn” – buffered acids at pH 5.2
- Instant brightening via stabilized vitamin C derivatives
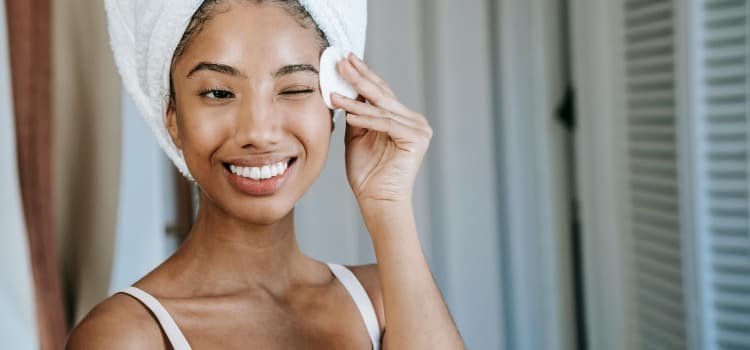
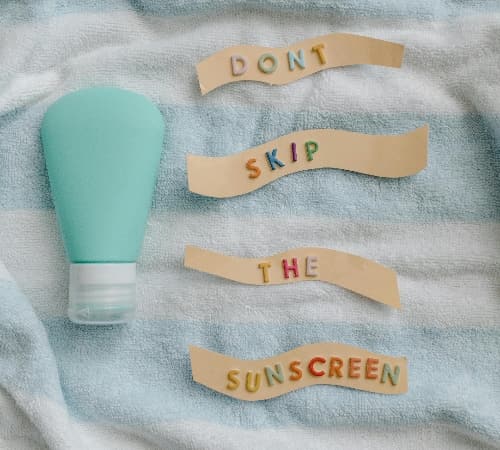
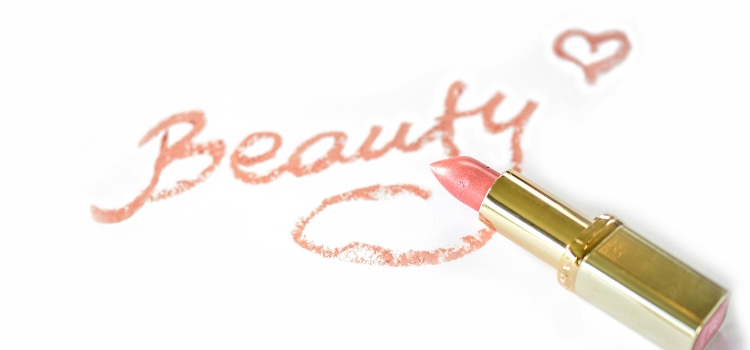
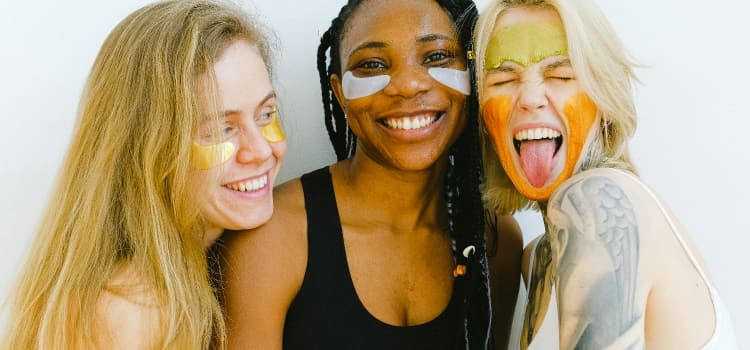